Procuring protective equipment and clothing for a workforce is just another task that may department heads and contract managers face.
Quite often it can go to the bottom of a pile of more pressing priorities with the easiest option being buying the products that the organisation and its operatives have always used.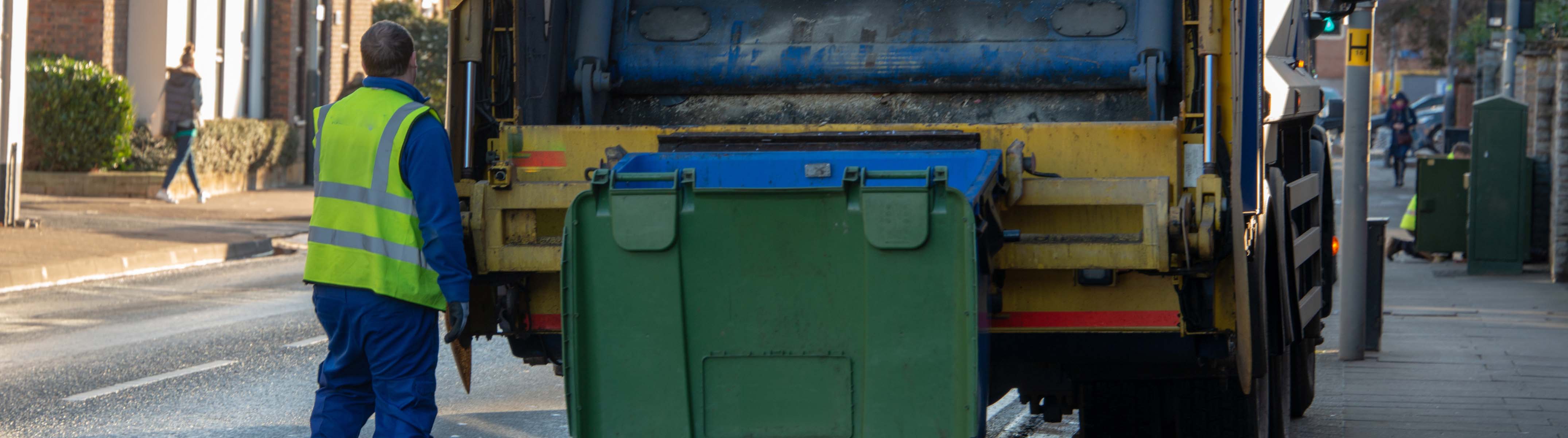