Getting hold of protective equipment and clothing has never been more uncertain. There are stock shortages and supply chain delays in a wide range of products from standard workwear items to disposable kit needed for protection against viruses.
This is having a really negative impact for a lot of our customers.
Teams who need clothing and PPE to operate effectively are being forced to compromise on what products that they are using or are having to wait for their supplies to arrive.
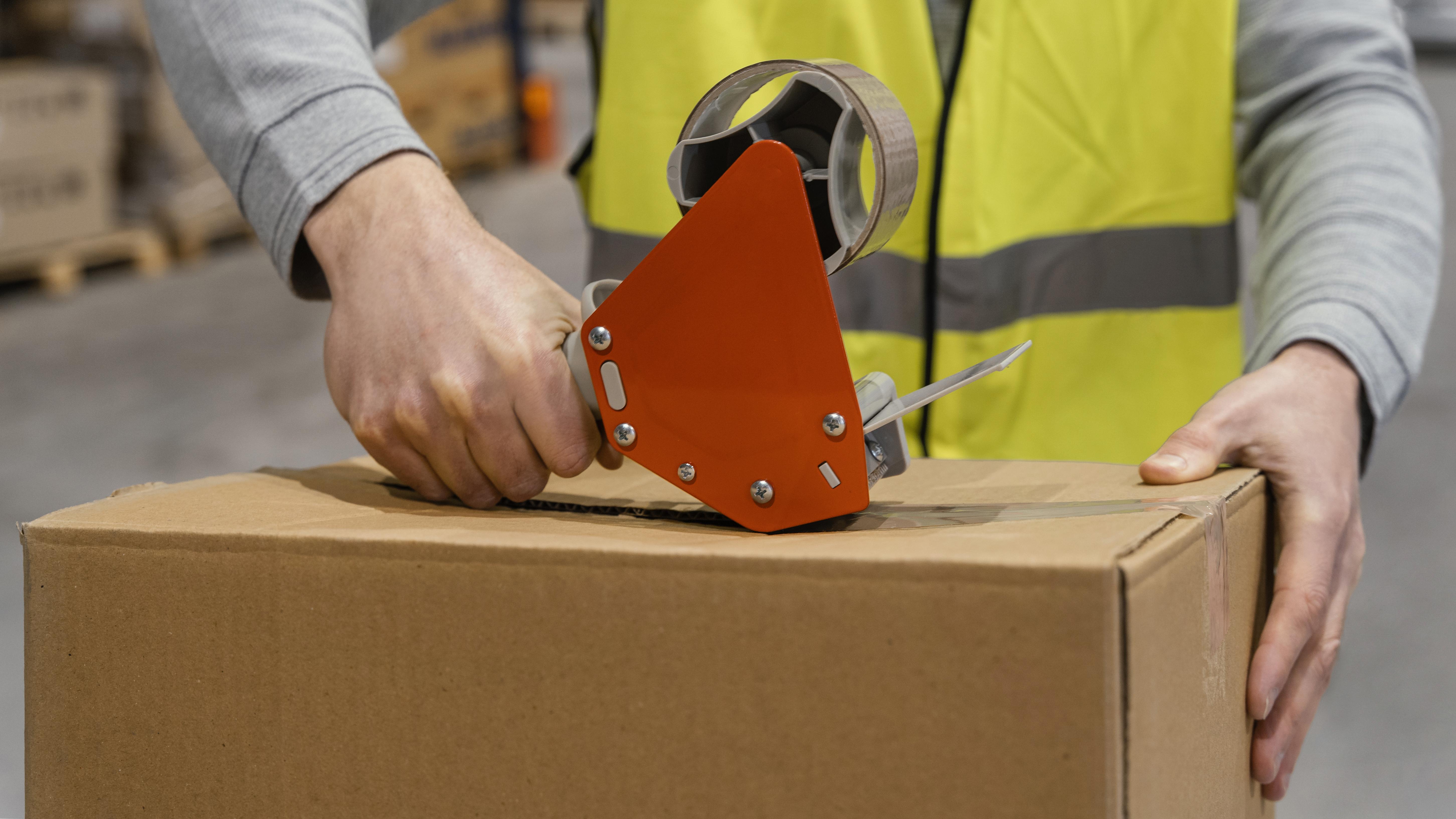
Why are these shortages occurring?
There are a variety of reasons:
The 3 most common causes are: a shortage of materials; staff shortages and transport delays.
The most pressing of these are the staff shortages and transport delays.
Staff shortages have been caused by the uncertainty that COVID-19 lockdowns have brought to the labour market, including the “pingdemic” of Summer 2021.
Transport delays are the biggest problem facing suppliers throughout the UK. Having been hit by staff shortages the transport and logistics sector also has the extra hassle of post-Brexit uncertainty and confusion to contend with.
At the current point the UK market is still transitioning away from the import arrangements in place before Brexit and the resulting increase in paperwork and workload is causing significant backlogs for many distributors throughout the UK. This is further complicated by the requirement to re-certify protective products under the new UKCA system that has replaced the original CE mark.
For customers who want to solve the problems caused by stock shortages there is no simple answer. The shortages exist across brands, products and suppliers. The most effective method of dealing with this particular problem is to work with a supplier that has: a robust stock management system; excess stocks with a plan to maintain them; an open and transparent approach to discussing supply chain issues with their customers.